我國鋰電池產(chǎn)業(yè)是否存在投資過剩的現(xiàn)象?導(dǎo)致的原因是什么?對(duì)產(chǎn)業(yè)造成哪些影響?未來,如何扭轉(zhuǎn)以往投資一窩蜂進(jìn)而導(dǎo)致產(chǎn)能過剩的通病,促進(jìn)行健康發(fā)展?
1個(gè)回答
-
邀請演講限于篇幅,僅對(duì)第二問和第三問做出解答。
一、結(jié)構(gòu)性產(chǎn)能過剩對(duì)動(dòng)力電池產(chǎn)業(yè)鏈的影響
1、增加行業(yè)負(fù)擔(dān)
結(jié)構(gòu)性產(chǎn)能過剩給行業(yè)帶來的負(fù)擔(dān)是持續(xù)的。一是已經(jīng)把大量的資金、人才資源集中在產(chǎn)能擴(kuò)張上,影響了技術(shù)研發(fā)的投入,為追求產(chǎn)量提升而輕視了產(chǎn)品質(zhì)量和性能提升。二是未來在產(chǎn)能整頓上還要花費(fèi)更多的精力,政府、市場、企業(yè)等各方還需在投資管理調(diào)控、監(jiān)管體系改革、準(zhǔn)入退出機(jī)制、企業(yè)協(xié)作與競爭機(jī)制等方面采取一系列改革措施,必定造成對(duì)技術(shù)創(chuàng)新、智能化水平提升的影響。當(dāng)前,日本松下宣稱在中國建立電池工廠,韓國三星SDI、LG Chem等企業(yè)瞄準(zhǔn)中國退出補(bǔ)貼后的市場,外資先進(jìn)企業(yè)在高端動(dòng)力電池市場上有非常大的競爭力。
2、延緩技術(shù)創(chuàng)新
實(shí)際上,日本、韓國在電池領(lǐng)域處于國際領(lǐng)先水平,企業(yè)數(shù)量少但各有其優(yōu)勢,在與車企形成戰(zhàn)略合作的同時(shí),以提升電池技術(shù)水平、降低成本為培養(yǎng)核心競爭力的目標(biāo)。相反,我國電池行業(yè)目前存在產(chǎn)能盲目擴(kuò)張的現(xiàn)象,整體呈現(xiàn)"多、散、亂"的局面,龍頭企業(yè)在產(chǎn)品技術(shù)水平、成本管控、生產(chǎn)管理體系上較少達(dá)到國際領(lǐng)先水平,中小企業(yè)陷在規(guī)模的困境中,盲目擴(kuò)張導(dǎo)致的產(chǎn)能過剩,造成了資本浪費(fèi)、研發(fā)積累不足、人才缺失。技術(shù)創(chuàng)新恰恰是離不開資金、研發(fā)、人才三大要素的支持,如何化解過剩產(chǎn)能成為動(dòng)力電池行業(yè)走向以技術(shù)導(dǎo)向的發(fā)展道路的當(dāng)務(wù)之急。
實(shí)際上,動(dòng)力電池屬于資金技術(shù)密集型產(chǎn)業(yè)。目前,國內(nèi)動(dòng)力電池相關(guān)企業(yè)整體研發(fā)實(shí)力偏弱,缺乏具有產(chǎn)業(yè)重大影響力的核心技術(shù)和專利,在高精尖技術(shù)方面,與發(fā)達(dá)國家企業(yè)仍存在較大差距。
據(jù)國際專利分類表(IPC)檢索,目前,全球動(dòng)力電池產(chǎn)業(yè)專利數(shù)量排名前10的企業(yè)被日、美、韓、德等國壟斷,這些企業(yè)專利數(shù)總計(jì)為3278件。其中,日本企業(yè)5家,占總數(shù)的50%,專利數(shù)占比達(dá)66.36%,豐田1家企業(yè)專利數(shù)占比高達(dá)38.71%;美、韓企業(yè)數(shù)量均為2家,各占總數(shù)的20%,專利數(shù)占比分別為16.44%和9.23%;德國僅博世1家企業(yè)入圍前10名,占總數(shù)的10%,專利數(shù)占比為7.97%。中國沒有企業(yè)入圍前10名,這表明,在動(dòng)力電池產(chǎn)業(yè)專利數(shù)量方面,我國企業(yè)與發(fā)達(dá)國家差距明顯,相關(guān)動(dòng)力電池企業(yè)市場競爭力較弱,我國動(dòng)力電池產(chǎn)業(yè)發(fā)展的專利壁壘尚未形成。
3、回收利用壓力大
盲目擴(kuò)張?jiān)斐闪说投水a(chǎn)能過剩,投入到市場的低端電池在技術(shù)性能、一致性、耐久性方面參差不齊,意味著我國動(dòng)力電池退役數(shù)量增加、退役品質(zhì)離散度大、回收利用難度增大。當(dāng)前我國動(dòng)力電池回收利用行業(yè)規(guī)模仍未形成,檢測標(biāo)準(zhǔn)不確定、梯次利用經(jīng)濟(jì)性和資源利用率較低,低端產(chǎn)能過剩勢必將造成回收利用行業(yè)的負(fù)擔(dān)。此外,產(chǎn)業(yè)的上游與下游之間的發(fā)展周期自身存在不同步的特點(diǎn),整車企業(yè)的產(chǎn)線建設(shè)周期一般為1.5-2年,動(dòng)力電池企業(yè)的產(chǎn)線建設(shè)周期約5年,而上游礦產(chǎn)資源的建設(shè)周期涉及勘探開采環(huán)節(jié),往往需要更長的建設(shè)時(shí)間,甚至高達(dá)10年,中間環(huán)節(jié)的動(dòng)力電池企業(yè)盲目擴(kuò)張將打破與上游、與下游的供需平衡,加劇產(chǎn)業(yè)鏈的不協(xié)調(diào)、不平衡問題。
儲(chǔ)能業(yè)務(wù)穩(wěn)步成長,將成為消化鋰離子電池過剩產(chǎn)能的重要去向。盡管儲(chǔ)能電池技術(shù)種類多樣,但鋰離子電池被認(rèn)為是最具前景的技術(shù),目前的主要障礙在于鋰電池較高的成本。根據(jù)儲(chǔ)能技術(shù)的市場需求,鋰電池成本降至0.9元/Wh時(shí)即具備應(yīng)用價(jià)值。未來幾年動(dòng)力電池的價(jià)格仍將持續(xù)走低,尤其是過剩比較嚴(yán)重的磷酸鐵鋰電池價(jià)格下行空間和壓力都較大,一旦儲(chǔ)能市場被打開,目前產(chǎn)能過剩的局面將迅速得到緩解乃至扭轉(zhuǎn)。
二、動(dòng)力電池行業(yè)健康發(fā)展的相關(guān)建議
1、加強(qiáng)產(chǎn)能預(yù)警,強(qiáng)化安全監(jiān)管
有效、真實(shí)的產(chǎn)能信息有助于投資者和企業(yè)合理決策,可建立產(chǎn)能發(fā)布和預(yù)警機(jī)制,由政府部門機(jī)構(gòu)或第三方非營利性組織進(jìn)行信息的核查與及時(shí)發(fā)布,杜絕"爛尾"工程和"占坑"行為,重點(diǎn)關(guān)注產(chǎn)能利用率和產(chǎn)能變化。
從保護(hù)消費(fèi)者利益出發(fā),加強(qiáng)違規(guī)電池產(chǎn)品的監(jiān)管力度,對(duì)出現(xiàn)電池質(zhì)量安全問題的企業(yè)進(jìn)行跟蹤調(diào)查,并實(shí)施有效的懲罰措施。
2、鼓勵(lì)市場化兼并重組
在淘汰低端產(chǎn)能中,市場將起到關(guān)鍵作用,技術(shù)落后、規(guī)模過小、形式分散的企業(yè)缺乏競爭力,在市場的優(yōu)勝劣汰機(jī)制下自然會(huì)被淘汰。隨著市場機(jī)制的發(fā)揮,企業(yè)間的兼并重組將加快步調(diào),企業(yè)的集中度和競爭力進(jìn)一步提高,要繼續(xù)發(fā)揮龍頭企業(yè)的引領(lǐng)和示范作用。
3、發(fā)展重心由擴(kuò)產(chǎn)轉(zhuǎn)向提質(zhì)降本和技術(shù)突破
當(dāng)前動(dòng)力電池主流企業(yè)的發(fā)展戰(zhàn)略重點(diǎn)不再是產(chǎn)能擴(kuò)張,而應(yīng)是如何優(yōu)化產(chǎn)能、通過核心技術(shù)創(chuàng)新和智能化水平提升實(shí)現(xiàn)產(chǎn)品的提質(zhì)降本,從根本上提升競爭力。我國動(dòng)力電池整體技術(shù)水平與日韓先進(jìn)企業(yè)相比仍存在差距。日本松下是特斯拉的特定供應(yīng)商,一款已經(jīng)量產(chǎn)的21700NCA三元鋰電池,單體能量密度300Wh/kg以上,成本約合1元/Wh,基本達(dá)到了我國2020年的發(fā)展目標(biāo)。且整車企業(yè)對(duì)動(dòng)力鋰電池的能量密度、循環(huán)壽命、安全性提出了更高的要求,動(dòng)力電池性能的提升亟待技術(shù)突破。因此,企業(yè)應(yīng)當(dāng)加大支持基礎(chǔ)研究,加速研究成果的轉(zhuǎn)化,重視人才的培養(yǎng),加強(qiáng)產(chǎn)學(xué)研政的協(xié)同發(fā)展,利用技術(shù)創(chuàng)新向高端領(lǐng)域集中,創(chuàng)造競爭優(yōu)勢。
4、提升智能制造水平,對(duì)于動(dòng)力電池的提質(zhì)降本、產(chǎn)能優(yōu)化具有關(guān)鍵作用
一是,我國動(dòng)力電池產(chǎn)業(yè)整體還是以"量"取勝,生產(chǎn)規(guī)模大但品質(zhì)不如日韓,尤其是一致性還存在較大差距;二是,動(dòng)力電池行業(yè)屬于制造業(yè)范疇,智能制造能有助于品質(zhì)的精準(zhǔn)控制,并降低生產(chǎn)成本。根據(jù)"真鋰研究"的統(tǒng)計(jì),國際龍頭企業(yè)的生產(chǎn)線自動(dòng)化率約85%,國內(nèi)的一線企業(yè)自動(dòng)化率不到60%,二三線企業(yè)更低平均不足30%;國際制造合格率90%,而國內(nèi)僅為70%-80%。動(dòng)力電池智能制造是基于大數(shù)據(jù)平臺(tái)的互聯(lián)互通互操作系統(tǒng),達(dá)到"工業(yè)4.0"水平。提升智能化、信息化、自動(dòng)化水平是一個(gè)系統(tǒng)的工程,仍然需要企業(yè)和政府持續(xù)的大力投入。鼓勵(lì)企業(yè)推進(jìn)動(dòng)力電池輕量化、標(biāo)準(zhǔn)化發(fā)展,在確保電池安全系數(shù)的前提下,提高同體積電池模組的能量密度,直接降低電池成本;推進(jìn)大數(shù)據(jù)、物聯(lián)網(wǎng)、互聯(lián)網(wǎng)等技術(shù)與動(dòng)力電池及其生產(chǎn)設(shè)備制造的融合發(fā)展,鼓勵(lì)企業(yè)建設(shè)動(dòng)力電池智能生產(chǎn)制造體系,實(shí)現(xiàn)智能制造產(chǎn)業(yè)升級(jí)。
5、注重戰(zhàn)略布局
一是向上游布局關(guān)鍵鋰鈷礦資源和關(guān)鍵材料,由于礦產(chǎn)資源分布的地域性特點(diǎn),國際化的戰(zhàn)略性資源綁定是動(dòng)力電池企業(yè)的重點(diǎn)方向。二是向下游與整車企業(yè)深度合作,充分了解配套電池的需求和要求,提高產(chǎn)能利用率和提升電池產(chǎn)品的技術(shù)水平。三是重視并盡早規(guī)劃動(dòng)力電池梯次利用及回收的環(huán)節(jié),打造電池產(chǎn)業(yè)鏈的閉環(huán)生態(tài)系統(tǒng),也是動(dòng)力電池企業(yè)幫助保護(hù)國家資源安全及環(huán)境安全的責(zé)任。 電池技術(shù)正處在快速發(fā)展的過程之中,它已經(jīng)成為主要國家競爭力的一個(gè)焦點(diǎn),這里既充滿機(jī)會(huì),也面臨著巨大的挑戰(zhàn)。拼生產(chǎn)規(guī)模只是淺層次的競爭,不斷提高自己的競爭地位最重要的是掌握核心技術(shù),而且有能力不斷創(chuàng)造核心技術(shù)。
G 評(píng)論掃一掃
打開app查看精彩評(píng)論收藏掃一掃
打開app查看精彩評(píng)論
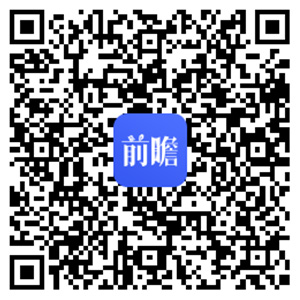
掃一掃
下載《前瞻經(jīng)濟(jì)學(xué)人APP》進(jìn)行提問
與資深行業(yè)研究員/經(jīng)濟(jì)學(xué)家互動(dòng)交流讓您成為更懂行業(yè)的人